VORBEREITUNGS-
VERFAHREN
FÜR FASERFORM
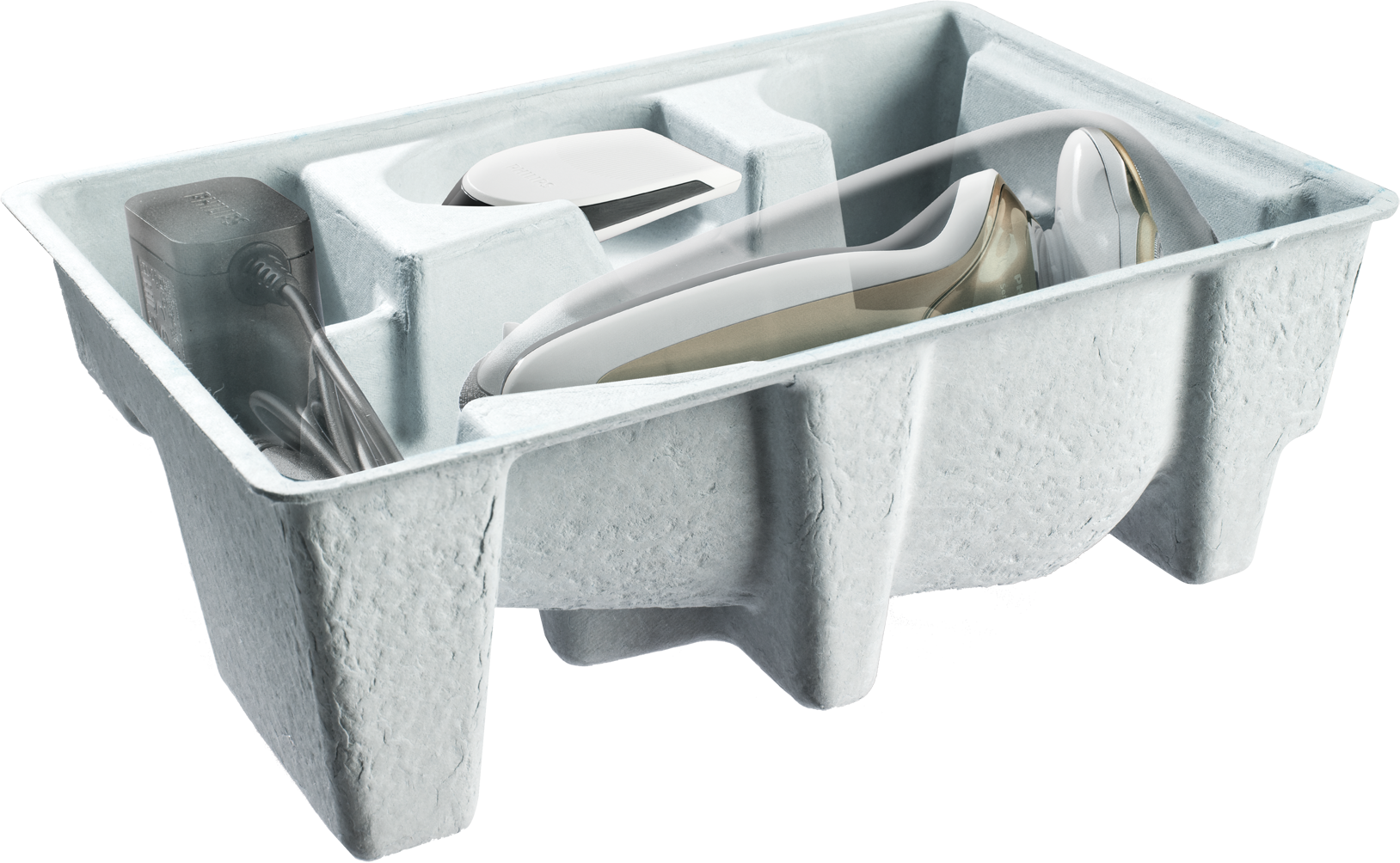
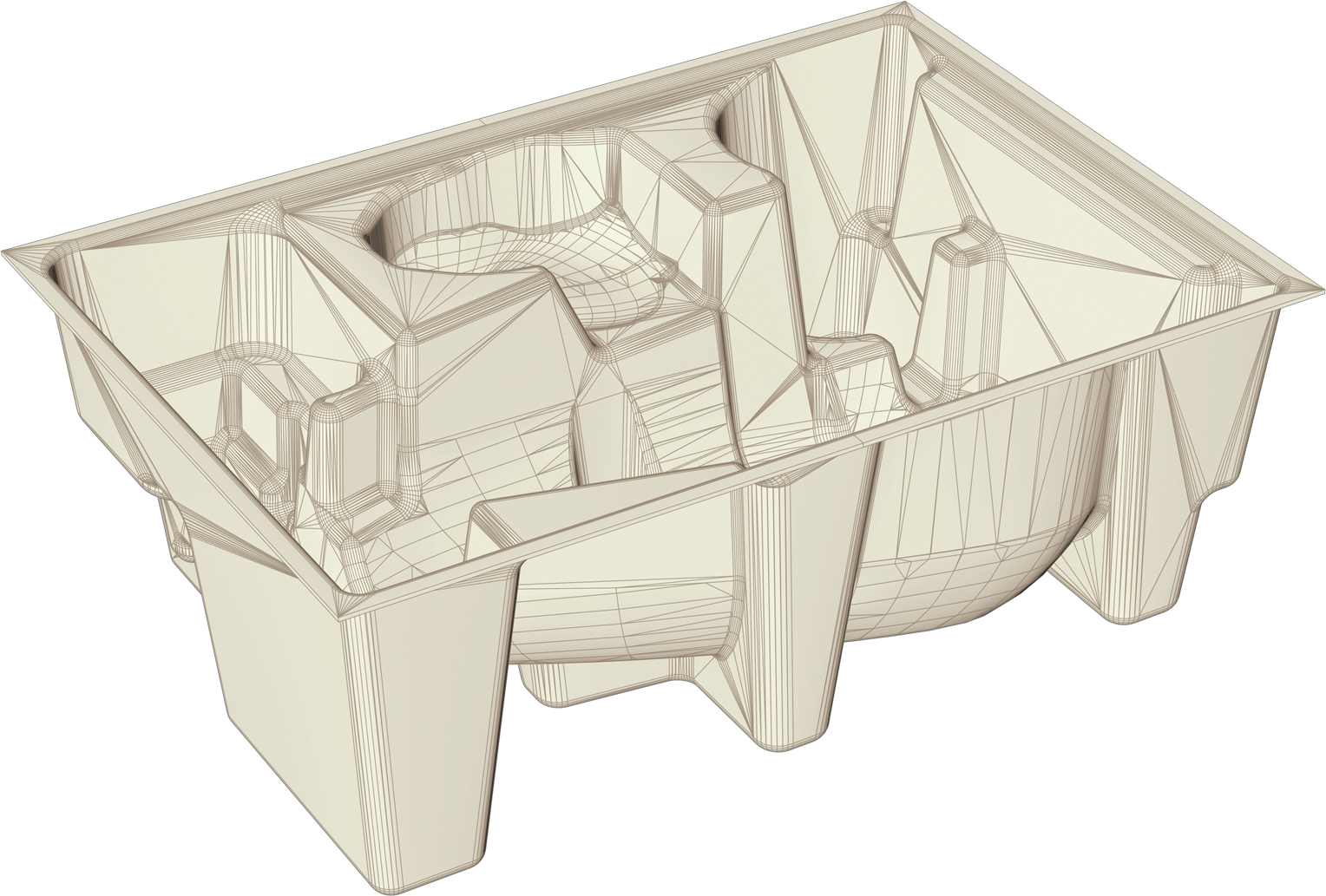
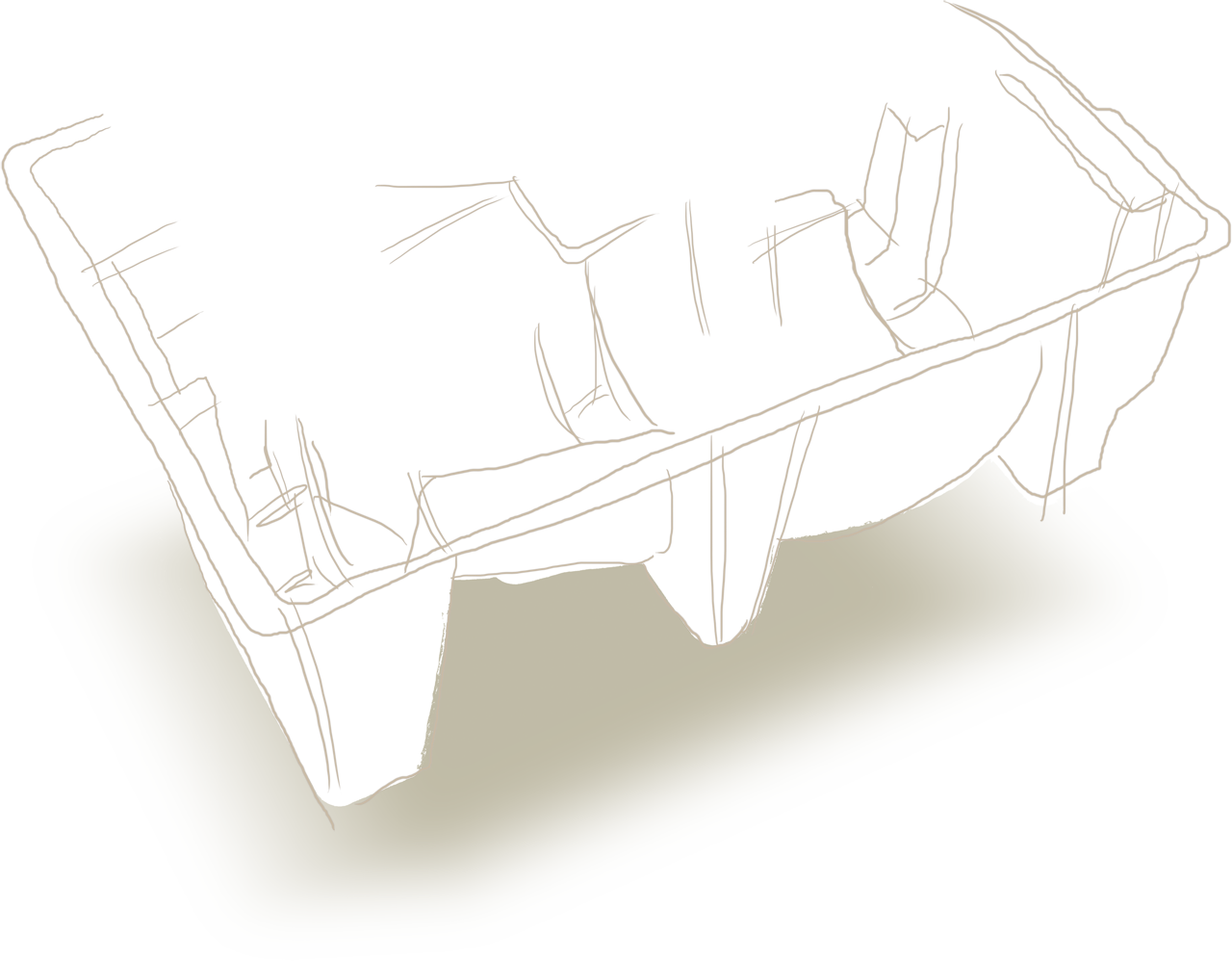
3. Fertiges Produkt
Im letzten Schritt wird eine Musterform hergestellt und anschließend ein echtes Muster produziert. Die Muster werden zur Überprüfung von Formen und für Falltests verwendet. Die Muster bestehen bereits aus dem gleichen Material und haben die gleiche Qualität wie die massenproduzierten Produkte.
2. 3D-Design
Im zweiten Vorbereitungsschritt wird ein 3D-Modell des Behälters in voller Größe erstellt. Für die Erstellung des 3D-Modells benötigen wir echte Muster oder Modelle des Verpackungsgegenstandes vom Kunden.
1. Entwurf
Nach Definition aller Eingabedaten wird eine einfache Skizze eines Behälters gezeichnet. Sie dient der anfänglichen Preisberechnung und zeigt das Verpackungsprinzip.
PRODUKTION
VERARBEITUNG VON FASERFORM
KONVENTIONELLE ANLAGE
Gesammeltes Altpapier (Pappkarton, Zeitungen) wird genau abgewogen und in den Stoffauflöser gegeben. Hier wird das Papier mit Wasser zu einer Konsistenz von 7 % gemischt und innerhalb von 15 bis 20 Minuten zu Faserstoff zerfasert. Diese wird durch eine zweistufige Filtrierung gepumpt. Im ersten Schritt werden starke Verunreinigungen (z. B. kleine Steine und Sand) herausgefiltert, im zweiten Filterschritt Klebeband und Kunststoff. Der gereinigte Faserstoff wird in Tanks aufbewahrt und besitzt eine Konsistenz von 4 %. Der letzte Schritt bei der Aufbereitung des Faserstoffs besteht darin, ihn zu mischen und zu verdünnen, bis er den erforderlichen Betriebsparametern entspricht. Das gesamte Verfahren wird per Computer kontrolliert.
Anschließend wird der Faserstoff in den Formbereich der Anlage gepumpt, wo er in Aluminiumformen gesaugt und zu einem Bandtrockner transportiert wird. Der Trocknungsprozess wird automatisch überwacht; während des Vorgangs werden Luftfeuchtigkeit, Temperatur und Menge der Trockenluft kontrolliert. Die Trocknungszeit des Produktes beträgt, abhängig von seiner Größe und der Materialdicke, zwischen 25 und 35 Minuten.
Wenn größere Oberflächenpräzision und Qualität notwendig sind, werden die Produkte in einer heißen Form nachgepresst. Temperaturen von 180 °C und Druck von 20 Tonnen bewirken eine sehr glatte Oberfläche. Zur exakten Einhaltung der äußeren Maße werden im letzten Produktionsschritt die Kanten zurechtgeschnitten.
THERMOFORMUNGSANLAGE
Zur Thermoformung von Produkten verwenden wir ausschließlich Neumaterialien ohne jegliche Verunreinigungen und Klebstoffe. Das Einsatzmaterial wird genau abgewogen und in den Stoffauflöser gegeben. Hier wird das Papier mit Wasser zu einer Konsistenz von 7-8 % gemischt und innerhalb von 15 bis 20 Minuten zu Faserstoff zerfasert. Der gereinigte Faserstoff wird in Edelstahltanks aufbewahrt und besitzt eine Konsistenz von 2 %. Der letzte Schritt bei der Aufbereitung des Faserstoffs besteht darin, ihn zu mischen und zu verdünnen, bis er den erforderlichen Betriebsparametern entspricht. Das gesamte Verfahren wird per Computer kontrolliert.
Anschließend wird der Faserstoff in den Formbereich der Anlage gepumpt, wo er in Aluminiumformen gesaugt und zu den Presswerkzeugen transportiert wird. Während des Trocknungsprozesses werden die Behälter mit einem hohen Druck von ca. 15 Tonnen gepresst. Die Temperatur der Instrumente wird automatisch überwacht und bei 150-220 °C gehalten. Die Trocknungszeit des Produktes liegt, abhängig von seiner Größe und der Materialdicke, zwischen 60 und 110 Sekunden.
Zur exakten Einhaltung der äußeren Maße werden im letzten Produktionsschritt die Kanten zurechtgeschnitten.